
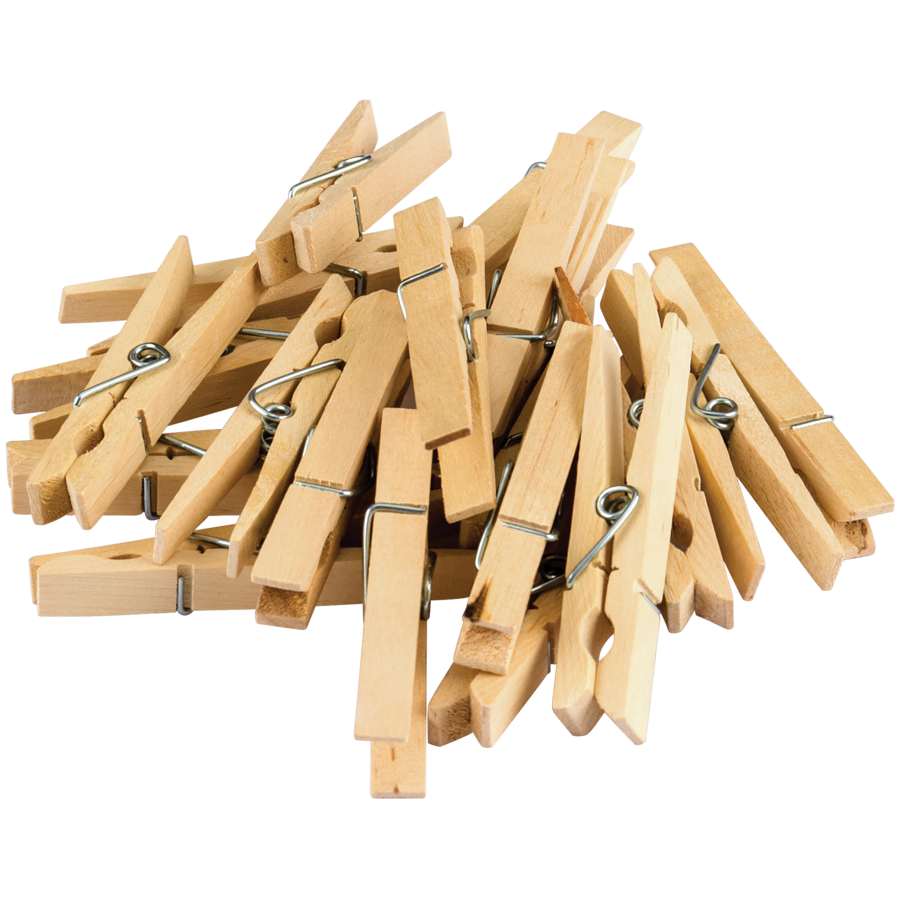
The profit margin was eaten into further by the increasing volume of cheap Chinese imports pleas for protective tariffs continued, but to no result. In this fashion, they managed to hang on through the following decades, in spite of a disastrous fire in 1978. However, the National Clothespin Company, who had previously moved from its original location across the street, and had been sold to a new owner, managed to stay in business by virtue of a contract with the F. The situation worsened after World War II, and the introduction of the electric clothes dryer diminished demand for clothespins, further damaging the industry the U.S.C. After World War I, cheap imports from Europe began to flood the market, leading to repeated calls for protective tariffs by Vermont, and the state industry went into decline in 1920, it cost 58 cents to manufacture one gross of clothespins in Vermont, while imported Swedish clothespins were sold for 48 cents a gross. Co., consuming 500,000 board-feet of lumber at the height of production. The new National Clothespin Company rapidly overtook the U.S.C.
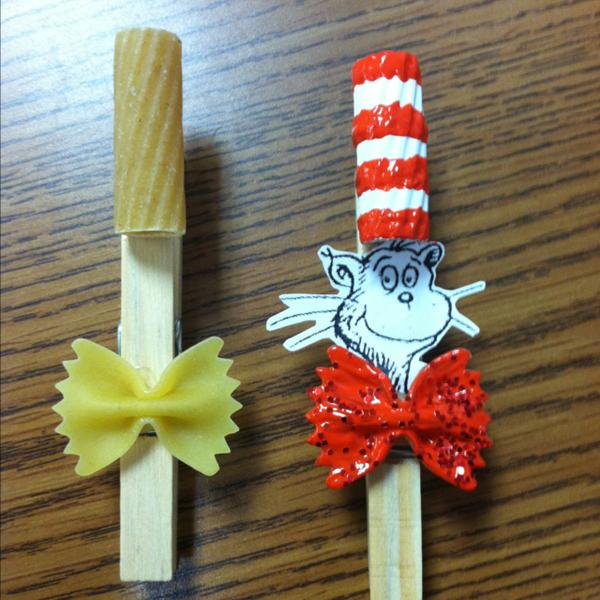
He left the company, and with a loan from a local entrepreneur opened a competing factory, across the street from the U.S.C. employees, devised a way in which clothespins could be manufactured more cheaply, by eliminating one of the coils in the "spring fulcrum". Vermonter Stephen Thomas, served as company president, and the company enjoyed a significant level of success, in spite of the competitors that rapidly sprang up in Waterbury and other places. Co.) opened in 1887 to manufacture Moore's improved design. The state of Vermont, and its capital of Montpelier, in particular, quickly became what The New York Times has called "The Silicon Valley of Clothespin Manufacturing", the United States Clothespin Company (U.S.C. This became the first successful spring-actuated clothespin, being manufactured and sold in huge quantities all across the United States. He added what he called a "coiled fulcrum" made from a single wire, this was the spring that held the wooden pieces together, acted as a spring forcing them to shut, and as a fulcrum on which the two halves could rock, eliminating the need for a separate component, and reducing manufacturing costs. The design by Smith was improved by Solon E.
